Our commitments
IMAGINING WITHOUT LIMITS
As the No. 1 luxury glass packaging manufacturer for Perfumery and Cosmetics and a pioneer in eco-design, our position requires us to uphold the highest standards of responsibility.
The emblem of our CSR commitment is the launch of our VERRE INFINI® in 2008, the first glass made from 100% PCR (post-consumer recycled) glass. Eco-friendly renovations of our facilities, ISO 14001 certified sites, continuous improvement of our sustainable performance system, and control of our carbon footprint: our environmental strategy aims to be visionary and exemplary for our employees, our communities, and our customers.
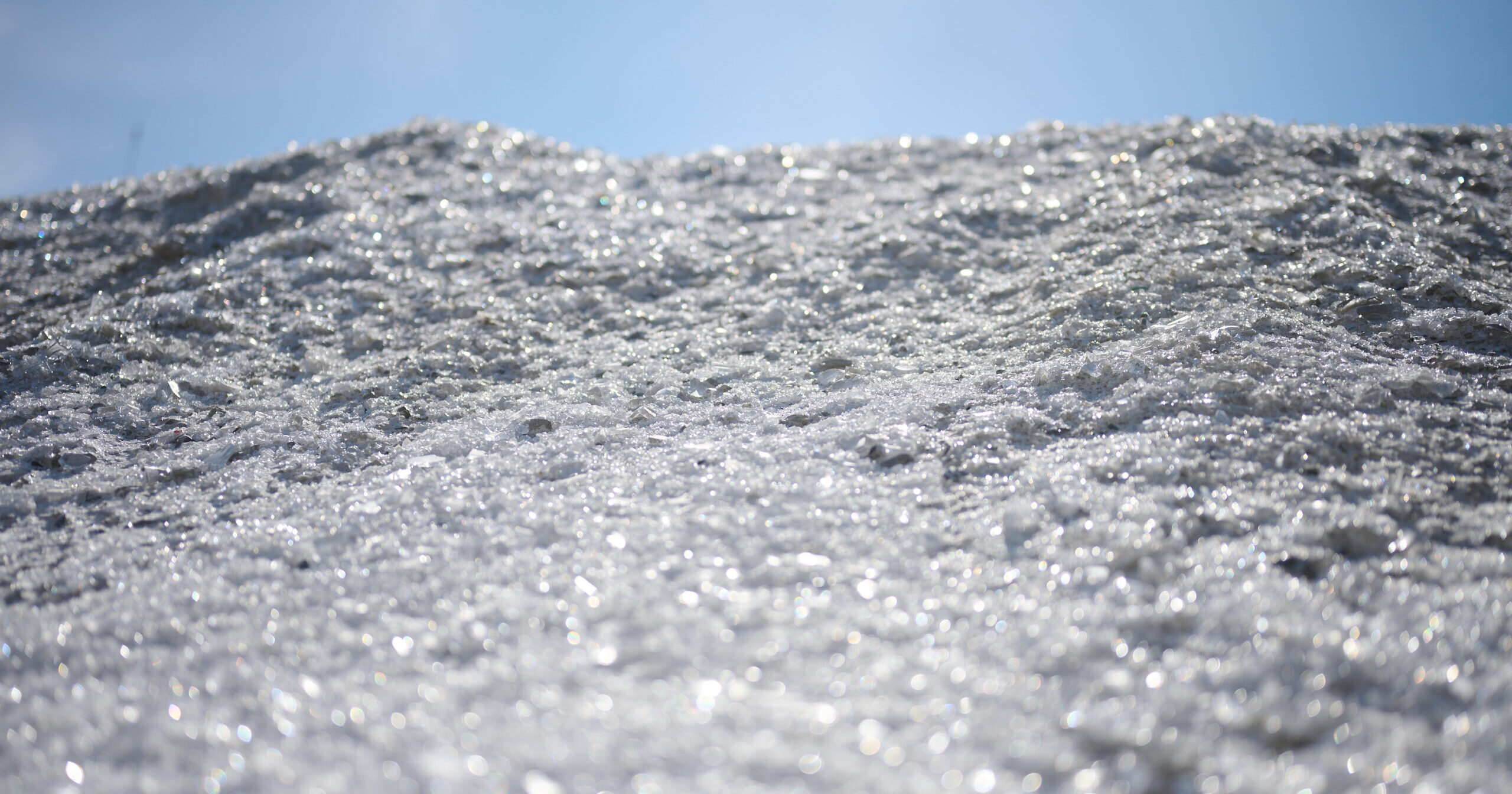
CSR strategy
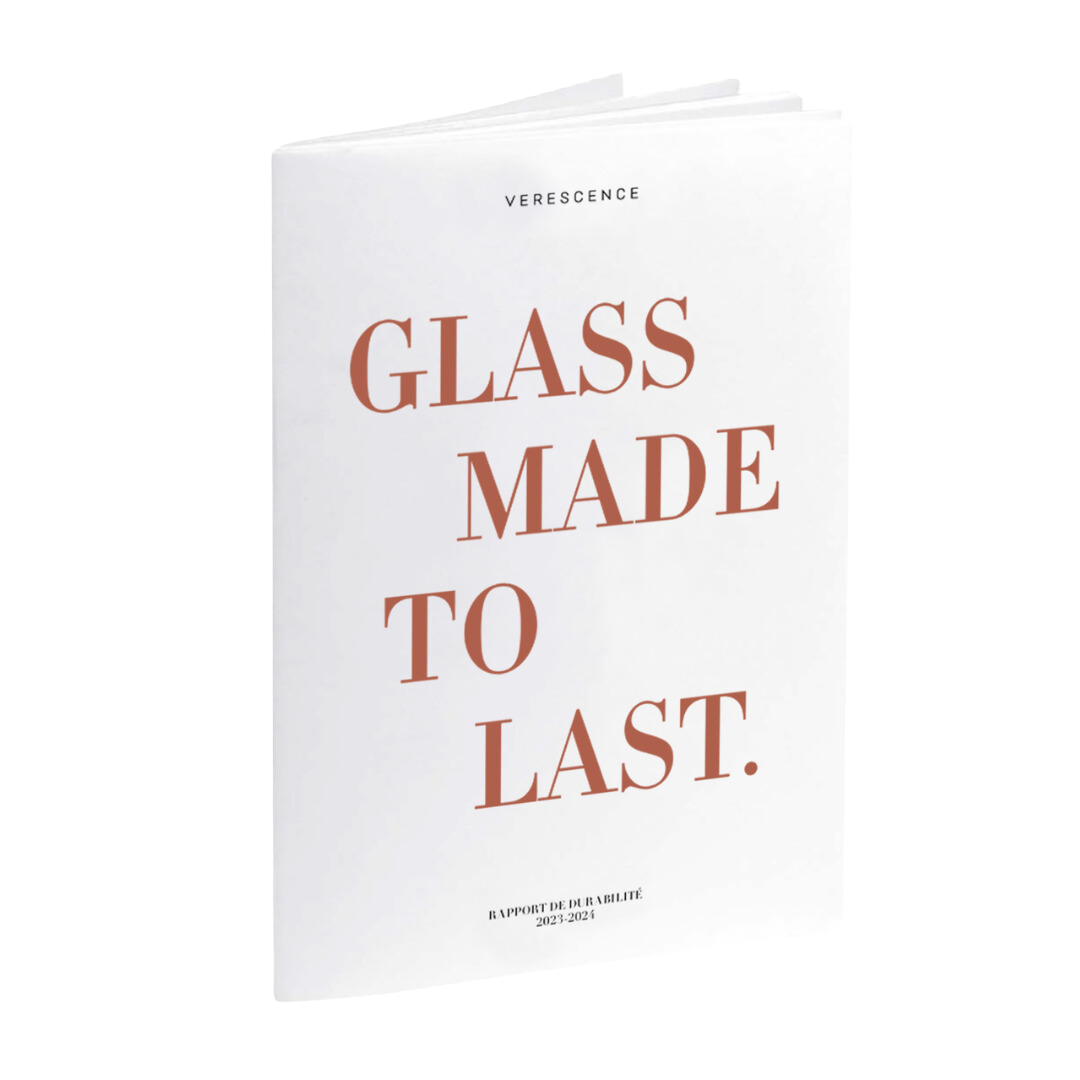
GLASS MADE TO LAST
Our CSR program, Glass Made to Last, is at the core of Verescence Group’s overall policy. Its three pillars, People First, Act for Society, and Eco Solutions, contribute to 15 of the 17 United Nations Sustainable Development Goals (SDGs).
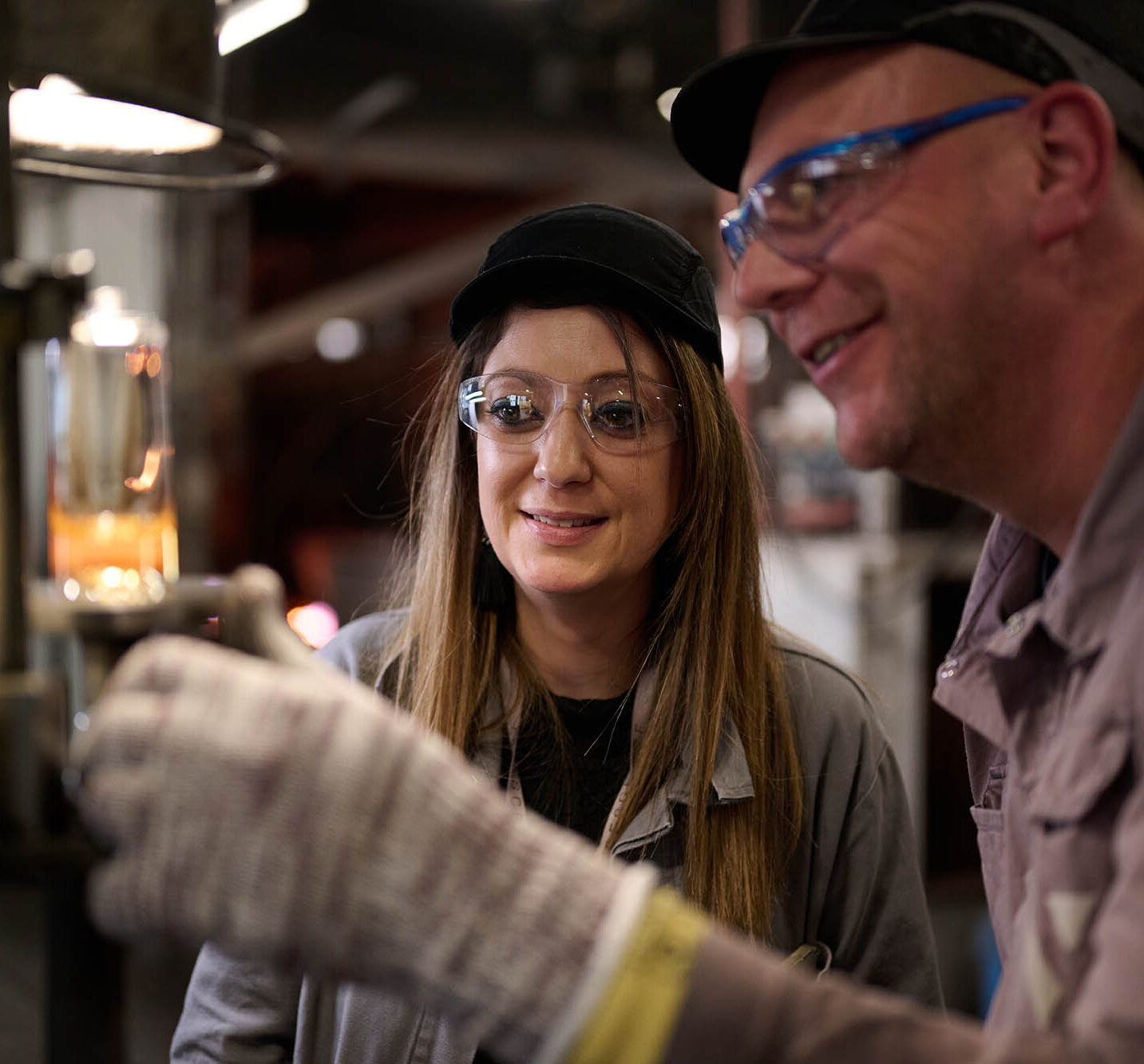
PEOPLE FIRST
Glass-making and finishing are not easily learned skills. Our professions are based on historical know-how that we maintain and evolve with new technologies. Because our Group is nothing without the talents that comprise it, our goal is to create the best possible environment to develop everyone’s potential while making safety, well-being, and diversity essential realities.
People First contributes to the following UN Sustainable Development Goals:
39%
of new hires were women in 2023
71%
of employees received training in 2023
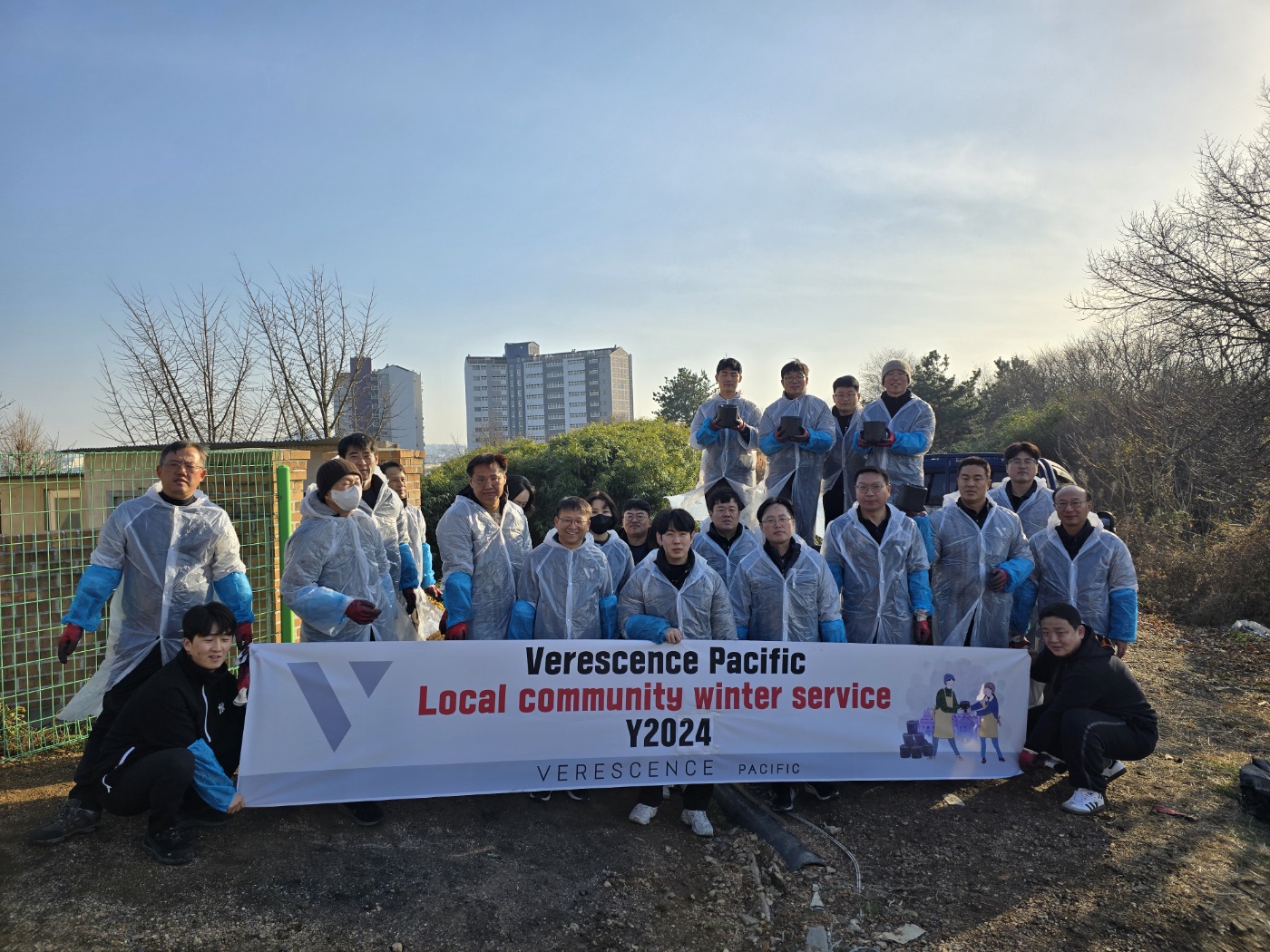
ACT FOR SOCIETY
Our global presence goes hand in hand with strong local roots. Community projects positively contribute to the ecosystems around us. We participate locally in “better living together” and socio-economic development. Our concept of responsibility includes preserving jobs on our sites, responsible purchasing, and business ethics.
Act for Society contributes to the following UN Sustainable Development Goals:
Verescence has been a signatory of the United Nations Global Compact since 2018
100%
of strategic suppliers have signed the CSR charter
97%
of purchases were local in 2023
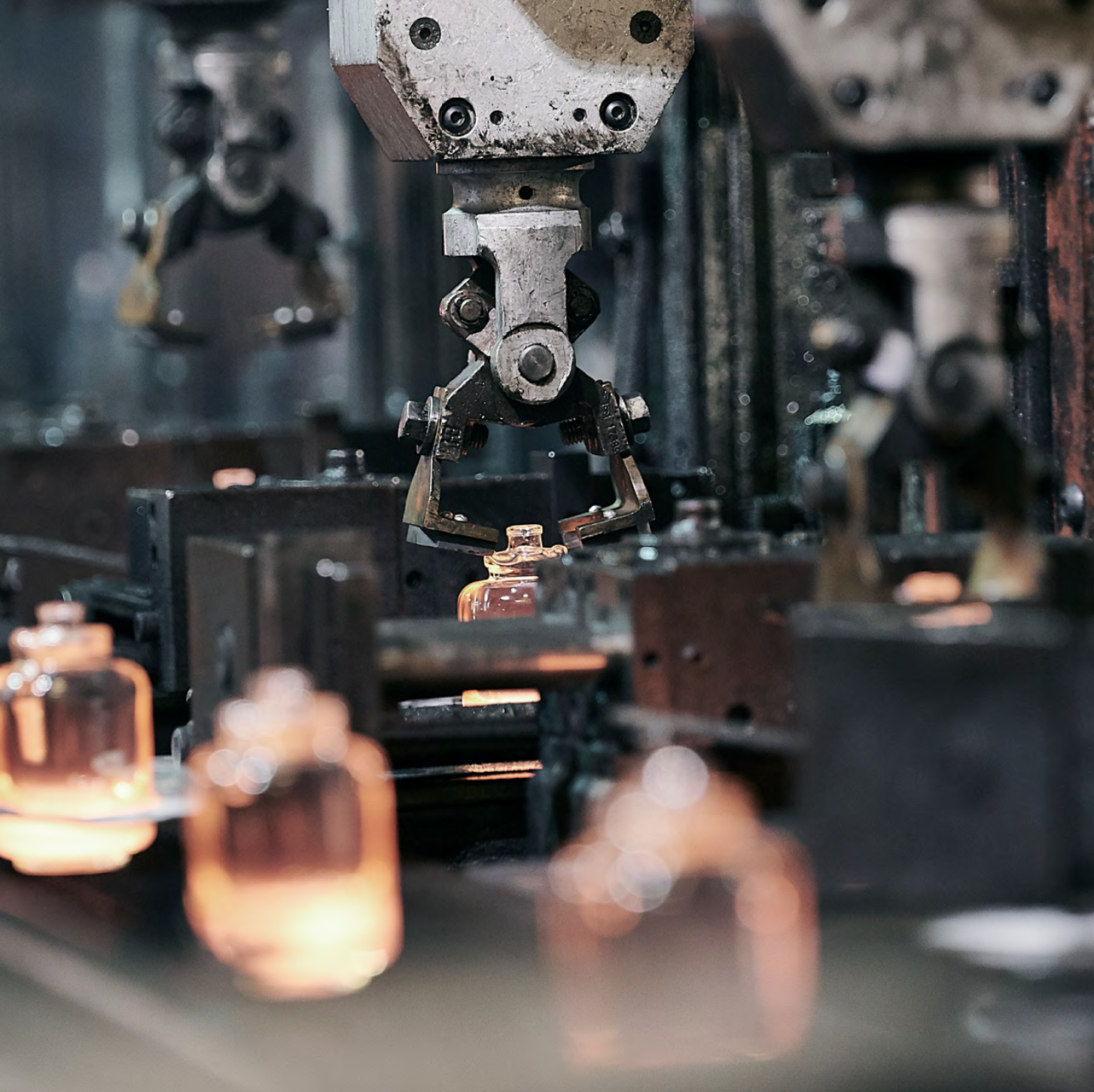
ECO SOLUTIONS
Infinitely recyclable without losing its properties, glass is an exceptional material that inspires us. We believe that developing planet-friendly processes and eco-designed products is compatible with luxury industry standards. Thus, we integrate ecological imperatives as a source of creativity and innovation.
Eco Solutions contributes to the following UN Sustainable Development Goals:
-19%
reduction in CO2 emissions (Scope 1 and 2) since 2017
91%
of waste recycled in 2023
98%
of water recycled in 2023
Ethics & Suppliers
EXCELLENCE IN OUR CSR APPROACH
Ethical and sustainable, our business practices foster long-term value creation and set a benchmark in the glass industry.
Our Code of Ethics and Conduct
Verescence adheres to the principles of the Universal Declaration of Human Rights, the International Labour Organization (ILO), and the Organisation for Economic Co-operation and Development (OECD).
Our company is committed to ensuring transparency in its activities and upholding rigorous ethics. You can report any concerns via our secure website: https://report.whistleb.com/en/verescence
Our Supplier CSR Charter
Throughout our value chain, we involve our strategic suppliers in our CSR policy. We prioritize local and short supply chains through a geographically structured organization.
A hundred companies, selected for their significant impact on Verescence’s social and environmental responsibility, are also subject to specific action plans tailored to their activities.
Decarbonization
TOWARDS CARBON NEUTRALITY
In response to energy challenges, we have implemented an energy-saving plan across all our sites worldwide.
These concrete initiatives aim to significantly reduce the consumption of various energy sources (gas, fuel, and electricity). Our CO2 emission reduction efforts are part of a long-term strategy. Our ambitious decarbonization plan is based on eco-responsible renovations of our industrial facilities, the use of new technologies (Industry 4.0), and a portfolio of products and services that bring ever-greater value to our customers.
2023 Carbon Footprint
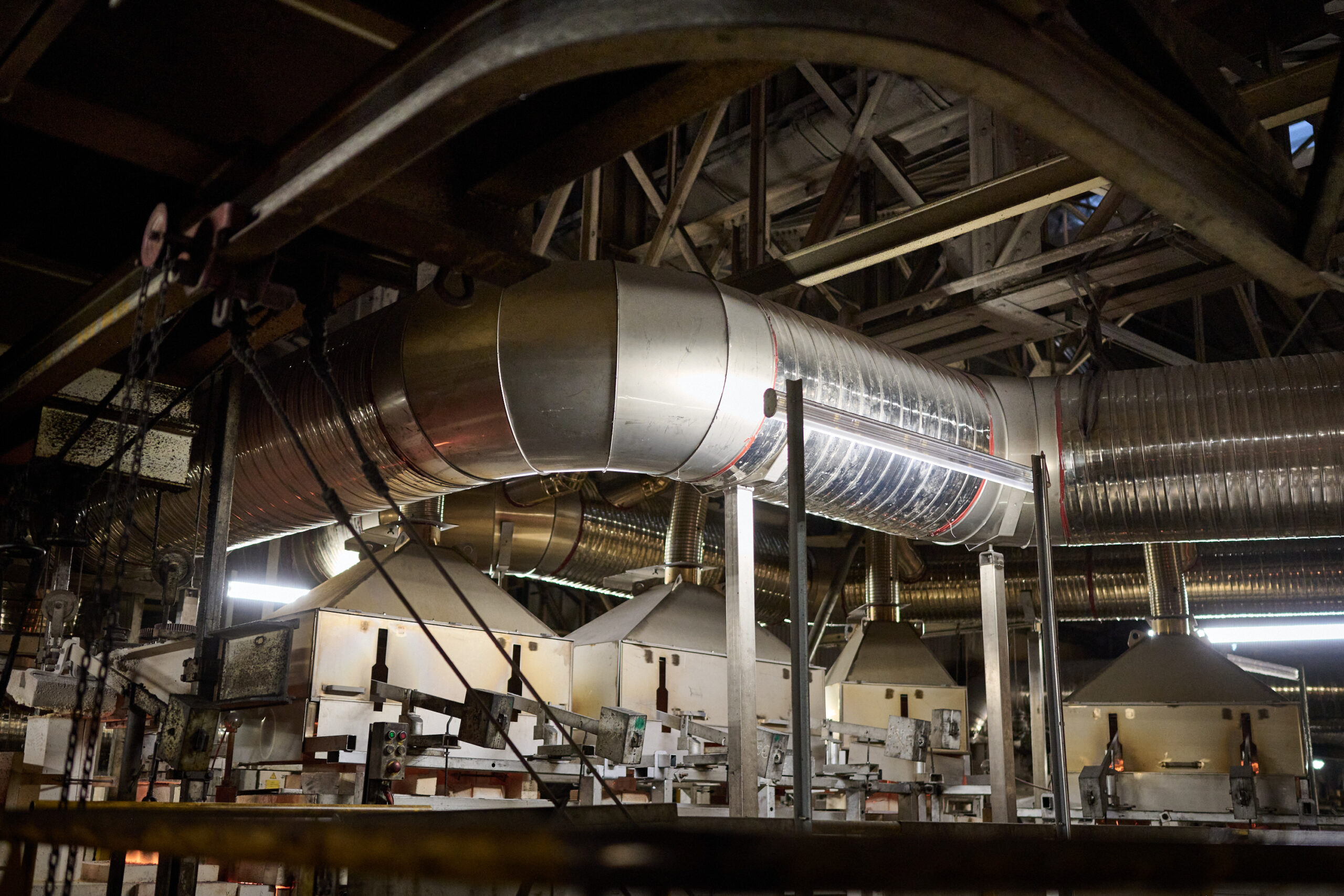
Waste Heat Recovery
Since 2023, our Mers-les-Bains site has been using an innovative waste heat recovery system from glass production. This project was carried out in collaboration with Clever Energies, a French company specializing in energy efficiency.
The innovation lies in the capture method, specifically above the feeders that channel the glass from the furnaces to the forming machines.
In 2023, we already observed a reduction of 2,000 tons of CO2, representing 4% of our decarbonization targets.
Decarbonizing our operations: our 2034 roadmap
CO2 Emissions Reduction Target (Scopes 1 and 2)
-63.7%
Reduction in direct and indirect CO2 emissions related to bottle manufacturing by 2034, in absolute terms compared to the 2019 baseline year
CO2 Emissions Reduction Target (Scope 3)
-37.5%
Reduction in indirect CO2 emissions from purchased goods & services, fuel and energy-related activities, and upstream transportation & distribution by 2034, in absolute terms compared to the 2019 baseline year
Our greenhouse gas (GHG) emissions reduction targets are validated by the Science Based Targets initiative (SBTi) and aligned with the ambition of the Paris Agreement to limit global warming to 1.5°C
Certifications & assessments
RECOGNIZED COMMITMENTS
To earn the preference of our customers, we strive for excellence while upholding our values and CSR commitments.
Certifications
The choice of certifying our Sustainable Performance System through a single body ensures uniform requirements and compliance with ISO standards (International Organization for Standardization), recognized by our customers and stakeholders in terms of Safety, Quality, Environment, Good Manufacturing Practices (GMP), and Energy Management.
100%
of our sites are certified: ISO 9001 (quality), ISO 22716 (GMP), ISO 14001 (environment), ISO 45001 (health & safety)
3
glass manufacturing sites are certified ISO 50001 (energy management)
CSR Assessments
Annual assessments by world-renowned organizations encourage us to go further in improving our CSR strategy and processes regarding CO2 emission reductions and water management.
2024 CDP thematic scores: Climate Change: A, Water Security: A-
In 2024, CDP, a reference in environmental reporting, confirmed our leadership in sustainability by awarding us an A for our climate change efforts and an A- for responsible water management.
2023 CDP Supply Chain score: A
Verescence ranks among the top companies receiving an A rating (leadership level) in the CDP’s Supplier Engagement Rating (SER), recognizing our efforts to mitigate climate risks within our supply chain.
PLATINUM EcoVadis Medal
In 2024, the EcoVadis rating agency awarded Verescence Platinum status. The Group ranks among the top 1% of companies worldwide for CSR performance across all industries.
Our three French sites, two North American sites, and Spanish site have maintained their Platinum medals for the fourth consecutive year, with scores exceeding 80%, while our South Korean subsidiary, Verescence Pacific, improved by two points, earning a Silver medal on its second evaluation.
At the moment
View all news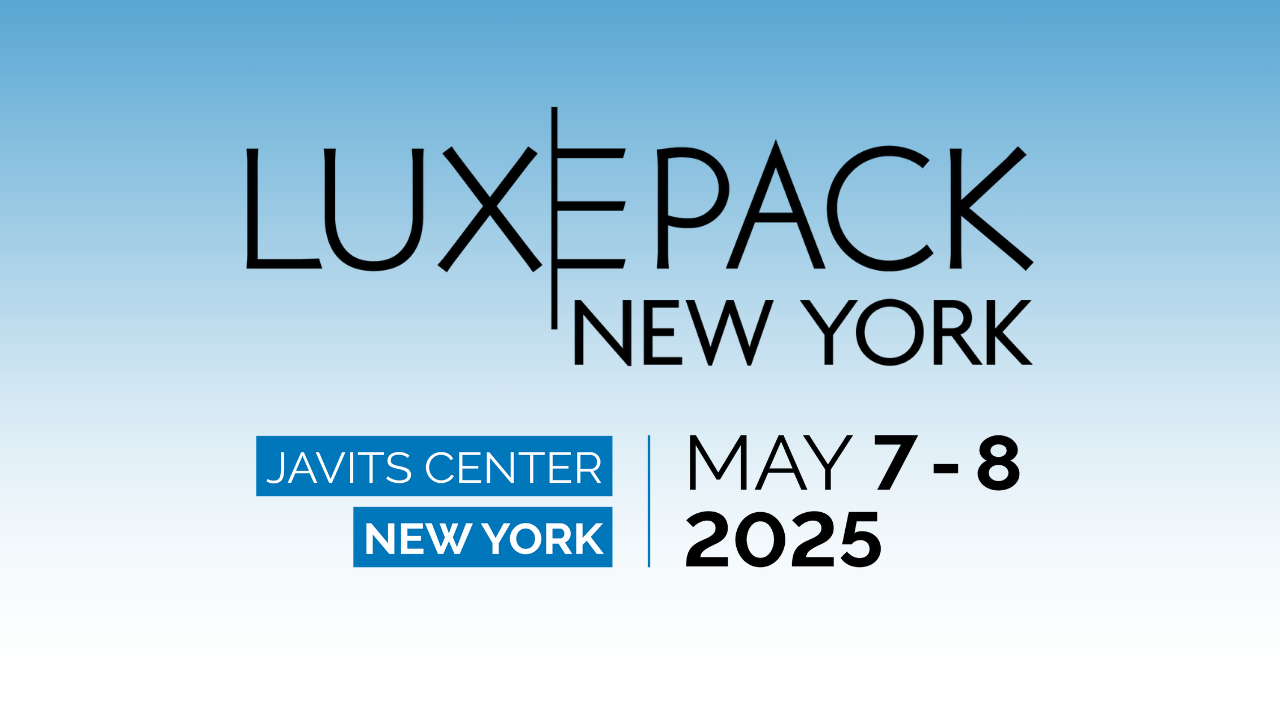
Verescence will be attending LUXE PACK New York on May 7-8, 2025, at the Javits Center.
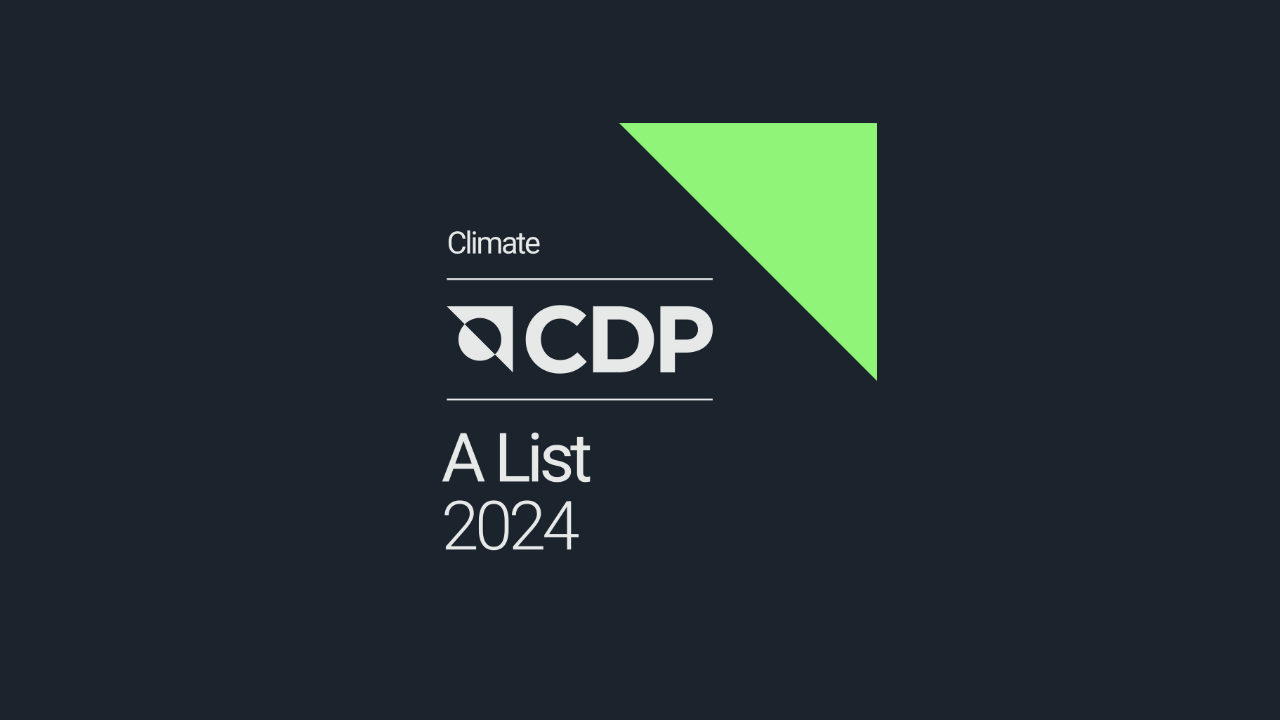
Verescence is once again featured on the prestigious CDP ‘A List’
The 2024 CDP sustainability ratings have been released, and we are proud to announce that Verescence has once again earned a place on the prestigious CDP A List!